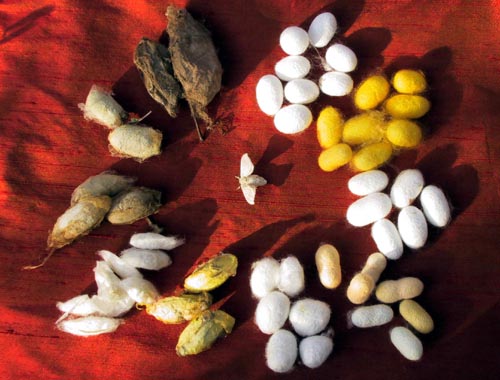 |
A Bombyx silkmoth
surrounded by different types
of cocoons. Clockwise from top:
four strains of Bombyx, dupion
(double) Bombyx cocoons, Tensan,
Eri, Oak Tussah, Polyphemus, and
Cecropia. |
Silk has been
revered as the Queen of Fibers for millennia.
Monks and princesses have smuggled its
secrets from country to country; bandits
have stolen it from camel-back caravans.
It is light, soft, shiny, and strong:
a cabled silk yarn has more strength,
per weight, than a cable of steel, but
silk can be made so light that it will
float on a breeze. Silk is more available
now for Western spinners than at any
time before in history; it can be purchased
in any form from raw cocoons and carded
top all the way to finished yarns, plus
special forms that are specific to silk,
like hankies and bricks.
Silk is a protein
fiber, secreted from a special gland
in the chin of a caterpillar. In the
wild, caterpillars use the silk to
build snug cocoons to protect them
while they change into pupae and then
into adult moths.
Bombyx mori, the domesticated
silkmoth, is the world's only truly domesticated insect.
The larvae are so dependent on human care that they
will starve to death if not hand-fed. They do not
exist, and never existed, in the wild; they were bred
up from wild species, like house cats and sweet corn.
Here's the story according to Confucius:
About 2800 B.C.E., the Empress Xi-Ling-Shi, wife of
the Yellow Emperor, was having tea in her garden one
afternoon. As she sat there, a white cocoon fell from
the mulberry tree into her steaming teacup. When she
fished it out with her chopsticks, it unwound into
soft, strong, shiny threads, and the clever Empress
realized that it could be fashioned into thread for
weaving.
Whether the actual discovery occurred
over tea or not, the Chinese managed to keep silk
a secret for many centuries. Silk could be sold or
traded, but the secret of its production was jealously
guarded, and anyone caught trying to smuggle the silkworms
and the knowledge of their cultivation out of China
was executed. It eventually spread to Korea and Japan,
and then to India, and finally to Europe during the
late middle ages, hidden in the headdresses of princesses
and the hollow walking staffs of monks. Silk centers
became established in many parts of Europe, including
Greece, Italy, France, and even England. With the
exploration of the New World, it spread to regions
of North and South America.


The stages in the life cycle of the
domestic silk moth.
From eggs to cocoons takes about four
to five weeks.
The domestic silkmoth takes about
six to eight weeks to complete one round of its life
cycle. Eggs are stored by refrigeration between cycles;
if you do this at home, the door of the refrigerator
stays around the right temperature. After they are
taken out of cold storage, it's a week to two weeks
before they hatch. Once hatched, they will eat mulberry
leaves for approximately four weeks until they spin
their cocoons. The caterpillars, or silkworms, will
change their skins four times, making five stages
called instars. The final instar caterpillars are
huge; they are often as thick and long as an adult's
pinkie finger. They spin their cocoons for about three
days, and then spend two to three weeks inside the
cocoons before emerging as moths. The moths use a
special enzyme to help dissolve the silk on one end
of the cocoon, and crawl out.
The moths are entirely flightless.
The females release a special pheromone that attracts
the males, who come running to mate with them. They
stay joined up for several hours to a day, and then
they separate and the female starts laying the 200-500
mustard-seed-sized eggs. The moths do not have mouths,
and cannot eat or drink, so they die once their stores
of energy and moisture are used up. This is not a
result of breeding; it's just the way silkmoths are.
Their entire life cycle, from eggs to eggs, takes
about six to eight weeks.
One of the wonders of Bombyx cocoons, is that they are spun by the caterpillar in a single unbroken
strand. This strand usually ranges between 600 and
1500 meters in length; 1500 meters is nearly a mile.
Most cocoon filaments aren't that long -- that's like
a Grand Champion cocoon -- but they definitely do
exist. The strand is called a bave; it is made of
two tiny sub-strands called brins. The brins are made
of a protein called fibroin, which is joined together
by another protein called sericin, or silk gum. The
sericin makes the cocoon shell tough and hard like
paper, and is often useful in silk processing to keep
the thread from shredding. Because they are made in
single strands, the cocoons can actually be unwound,
a process called reeling. In order to reel the cocoons,
the pupa inside must be stifled, or killed, with heat
so that it does not emerge and break a hole in that
long fiber. Stifling is an issue for many strict vegetarians
and vegans, who won't wear or work with this kind
of silk because the bugs die in the process.
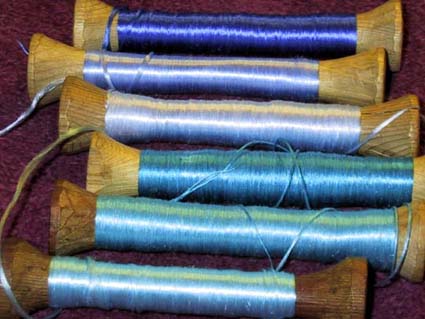 |
Spools
of organzine and tram. |
The individual bave is very fine,
about two and a quarter million yards per pound. At this weight, it's too fine to be
useful by itself, so the baves from multiple cocoons,
from 6 to 100 depending on the end use, are reeled
together. In order to unwind the cocoons, they are soaked in hot
water, and the ends are located with a brush.
Reeling makes a fine, shiny fiber referred to as raw
silk filament. The multiple baves in the filament
are joined together by the sericin, which is softened
but not dissolved by the hot water, so that raw silk
looks like a single thread.
Raw silk can be made into a variety of beautiful and
useful yarns; of these, only a few are of interest
to the hand-spinner and knitter. Organzine is a two-or-more
ply yarn which is made by twisting the raw silk filaments
one direction and then plying them back the other
direction; it is strong and fairly shiny. Most of
the fine knitting silks are organzine yarns. Tram
is made by twisting the fibers more gently in only
one direction to make a soft singles yarn; tram is
more often used for weaving weft, and for embroidery
where it does not need to bear a lot of stress. Tram
is the most shiny of silk yarns, but doesn't handle
tension or abrasion as well as organzine. Tram and
organzine yarns may be useful to you as a binder thread
when spinning specialty yarns, or can be plied up
with other fibers to add shine and color. Because
they are not drafted from short fibers, these yarns
are called reeled or "thrown" silks. Throwing refers
to the twisting process; it is done in industry by
special machines, but it can also be done at home
using a spindle or a wheel. The general rule of thumb
is that more twist means more strength, but less shine.
Softly twisted silks sometimes pill or snag easily.
Tightly twisted silks can be hard or harsh in the
hand; many spinners remark on this with the sari silk
waste yarns, which are made from the off-cuts of silk
weaving looms. A lot of silk fabrics are made using
organzine for the warp and tram for the weft; this
produces a strong fabric but with a high sheen.
The next step for most silks is
degumming. Degumming is a simmering process using
an alkaline surfactant bath that removes the sericin,
leaving the silk soft and shiny. Some commercial silk
processors use an enzyme to assist with this, but
others don't. Just like scouring the lanolin out of
wool, degumming can be a progressive process -- you
can partially, mostly, or fully degum silk. Most reeled
silks are degummed in the yarn stage, before dyeing.
Others are left raw, with the gum in. Certain fabrics
are degummed after weaving, because the gum protects
the thread from abrasion on the loom, but some are
left raw, like silk organza. The gum gives the silk
a stiff hand, which can be useful in certain situations,
especially when the fabric should be sheer but fairly
stiff.
A note about the term "raw
silk" -- raw silk is like raw food -- it hasn't
been cooked (degummed). Lots of people refer
to a yarn or fabric as "raw silk" when what
they really mean is one of three totally different
things: spun silk (which is almost always degummed),
silk noil (which is, again, almost always degummed)
or dupioni silk, which is usually degummed.
Dupioni silk is made by hand-reeling cocoons
where two silkworms have spun one joint-effort
cocoon; it has characteristic lumps and slubs,
but a lot of sheen.
My recipe for degumming
bath:
1/4 cup Orvus paste
-- You can substitute 1/2; cup of a non-fancy shampoo, or dish detergent,
but Orvus is the best.
1/4 cup Washing Soda -- This is also called Soda Ash or Sodium Carbonate -- Arm and
Hammer makes a good brand, in a yellow
and red box; it's in the aisle where the
Borax and the stain treatments are, next
to the laundry detergents. It's not the
same as baking soda (sodium bicarbonate).
This is a mild alkaline.
Enough water to make
1 gallon -- use distilled if your tap is full of minerals.
|
Mix the solution up [see recipe
at right]. You can use a gallon water jug, and
just pour in the chemicals and fill it up with
water. The solution does not go bad, but it
will settle, so shake before using. Fill a crafts-only
kettle with enough solution to float whatever
you're degumming, and bring the solution to
a boil. Turn it down so that it stays hot, but
does NOT bubble any more. Introduce the yarn,
waste, cocoons, or whatever you're degumming,
and let it simmer for 30 to 45 minutes, gently
moving the fiber or yarn a couple of times,
but never stirring. Make sure the kettle stays
hot but does not boil. Silk will not felt or full, although the yarn
may bloom somewhat. Cocoons and other loose
fiber can, however, mat up if stirred or boiled.
For skeins of yarn, it helps if you use a stick
or a stainless spoon to lower the skein into
the kettle, and leave the stick/spoon in the
kettle with the skein on it. It makes it easier
to pull it out again, and keeps the skein from
tangling. Most spun silk yarns and fibers won't
need degumming; they are typically degummed
before the spinning process.
Silk fibers naturally
want to be in a slightly acid situation.
After dyeing, washing, or especially
degumming, it is important to re-acidify
the silk with a mild acid. I usually
prefer citric acid, because it is
cheap and doesn't smell; use about
a tablespoon per a gallon or so of
water as a rinse. Vinegar also works;
use a quarter-cup "glug" or so per
gallon of water. Silk has a special
characteristic called "scroop" --
this is often referred to as a crunchy
feel, and it also has a rustly sound.
Scroop is like the feeling of squeezing
a big bag of cornstarch or powdered
sugar, or stepping down into very
powdery snow. Acid helps restore the
scroop to silk, as well as keeping
it happy and in good shape. Silks
which are dyed with alkaline dyes
or stored in alkaline conditions for
too long can shatter -- you go to
pick up a piece of silk fabric, and
it comes up in dozens of tiny bits.
I got to see this when I worked for
a history museum, in some beautiful
old dresses. Unfortunately, shattered
silk is almost impossible to repair,
because there's no strength to it
any more.
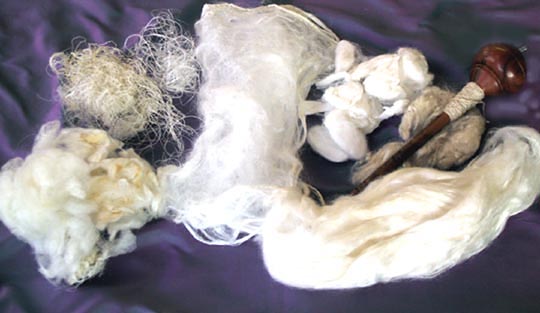
Different forms
of silk fiber. From left: Cocoon strippings,
reeler's waste, throwster's waste,
silk hanky, degummed cocoons, carded Polyphemus silk
batt (with Bellwether silk spindle),
combed Eri silk top. All fibers are
from the author's silkworms.
The vast majority of the silk used
by hand spinners is waste from the reeling process.
Cocoons that are cut open for breeding, those that
are stained or faulty, and all sorts of different
snagged or cut bits get turned into spinning fiber
and spun yarns. There are dozens of different machines
that handle the reeled silk during the various winding
and twisting processes; each one of them produces
a distinct variety of waste. Some of the longer, better-quality
waste fibers are degummed, carded, and then combed
to make silk sliver or top; these make the shiniest
and most expensive spun silk yarns. Most of the silk
that you can buy for hand spinning is this sliver/top
form. In terms of spinning, it is handled much like
wool or alpaca, although the silk lacks scales, and
can be more slippery and may need a firmer grip. It
is often easier and faster to spin silk from the fold;
pull on the end of the top, removing a little bundle
of fibers, and fold it over the fingertip.
Silk bricks are a preparation that
is made after the silk is combed into a rectangle,
but before it is made into tops; they are folded tightly
and compacted into a little tight rectangle, thus
the name. Cocoons that are used for breeding are typically
cut open on one end to remove the pupa, so that the
moths don't pee on the cocoons (lovely, but true)
-- these can be degummed, and then turned into hankies
or caps or left as degummed cocoons, which look like
compacted cotton balls. The cut cocoons are also used
without degumming to make decorative accents and jewelry.
Hankies, also called mawatas, are stretched on a square
that looks like a picture frame with spikes on the
corners; caps are stretched over an upside-down U
of bamboo. Amy Singer wrote an article
in the Winter issue about how to attenuate and
spin silk caps into yarn. Some companies also offer
waste silk fiber called throwster's waste -- this
is made of bits of thread that are waste from the
throwing frames which twist the silk. Some throwster's
waste is highly twisted, some is fairly soft -- it's
basically a difference between whether it got snarled
on the bobbin before the twisting part, or after.
Occasionally throwster's waste is sold in the gum,
but usually in the USA we get it degummed, and it
looks kind of like washed cotton fiber. If you get
waste that is gummy, it will make a smoother, less
hairy yarn if you degum first and spin afterward.
It's nicer on your fingers that way, too.
Species silks, or
"wild" (actually semi-domesticated)
silks, used to be very hard to find.
Nowadays, hand knitters and spinners
can get Tussah fibers and yarns in
a wide range of colors and preparations,
and some vendors even offer Eri and
Muga yarns and fibers. Each of these
is produced by a different species
of moth. In India, which is where
most of the wild silks are produced,
they are called "vanya"
silks; these silks each have a distinctive
feel and color, and they are a treat
for the hand spinner.
 |
Tussah silkworms
are much more hardy and wild than
Bombyx. This is a Chinese Oak
Tussah caterpillar in its fifth
and final larval stage. |
Tussah (also spelled
Tasar, Tusseh, Tussore, Tussar) is
the most popular and available type
of wild silk here in the US. The designation
actually covers a few different species
of related moths, and biologists often
use the term to refer to the whole
genus. There are three main types
of silk-producing tussah: the tropical
tussah moth, Antheraea mylitta, lives in India and eats two trees called Asan
and Arjun; the temperate or oak tussah
moth, Antheraea pernyi, lives in China and eats oak, and the Himalayan
silkmoth, Antheraea roylei,
lives in the Himalayan forest region
and eats oak.
 |
Chinese
Oak Tussah moths. Female above,
male below. Tussah moths are strong
fliers, and can have a wingspan
of six inches. |
A hybrid between roylei and pernyi has been created, called Antheraea proylei; it eats oak too, and makes a bigger cocoon with more
silk. The hybrid moths are being used in Indian sericulture
establishments, and they are being raised far outside
of their natural range.
Tussah silks tend to be more textured than Bombyx, and they range in color from a pale rosy tan through
a dark golden brown. Some varieties of tussah silk
are bleached with peroxides to make them whiter so
that they can be dyed to paler shades; I personally
like the color of the natural silk. It takes dye beautifully
-- just keep in mind that the original color affects
the shades of whatever you dye over it!
Tussah caterpillars are raised outdoors on huge plantations
of oak, Asan, and Arjun trees (according to their
type and climate), and the cocoons can get nearly
as large as a small hen's egg. The cocoons of the
tropical tussah moth have a long peduncle, or stem,
which the caterpillar makes by wrapping silk onto
the stem of a leaf; the other types of tussah moth
make a more compact cocoon with no stem. The tussah
moths are large, with a wingspan usually of five or
six inches, and are strong fliers. Although they are
semi-domesticated, they have not been bred as much
or as vigorously as the Bombyx, so they're
much more hardy and need to live outside.
Muga silk comes from another moth
in the tussah family. It is grown primarily in the
Brahmaputra valley area of India, although efforts
are being made to expand mugaculture into other parts
of tropical India. The muga caterpillar spins a golden
silk which is highly prized, and the reeled silks
hardly ever leave India. But now, hand spinners in
the West can get muga fiber to spin into yarn. It
is darker and more yellow in color than most tussah
silk, although personally it seems to me more brassy
or bronze than gold. From the samples I've handled,
muga also has a slightly more scroopy feel in the
hand than tussah.
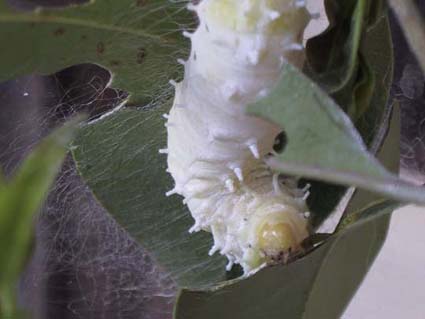 |
The
Eri silkworm from India spins
a fine, soft silk with a creamy
white color. |
Eri is the other well-known wild
silk. It is not nearly as well represented in Western
markets, but it is widely used in India. The moth,
Samia ricini,
which produces Eri silk is not closely related to
the Tussah or Bombyx moths, and like Bombyx, it has been bred to the point that it is essentially
a domesticated insect. Eri caterpillars eat a number
of plants, including castor bean, manioc (tapioca)
and kesseru. Because these are food crops, Eri silk
raising is often used alongside of the food production,
as a valuable side product.
Eri is rarely seen as a silk spinning fiber, although
some specialty yarn shops (like Habu Textiles in New
York) do carry Eri yarns. Eri silk is popular with
many people who object to Bombyx silk because of the moths being killed; because of
the way the Eri caterpillar spins its cocoon, the
silk cannot be reeled, so the moths are often allowed
to emerge instead of being stifled. The spun yarns
are often more "cottony" than most Bombyx silks, although
some roving-spun Eri yarns can be very soft and shiny.
The Jain Buddhists refer to this as "ahimsa" silk,
named after the principle of not harming any living
thing. Many Westerners call this, and certain other
types of silk raised without killing the moths, "peace
silk."
There are wild silkmoths in America
and Europe as well. It's a little extra work, but
yarn can be made from the cocoons of several of the
wild species. They take longer to degum than Bombyx silk, up to two hours for some types. I've raised half
a dozen species of wild North American silkmoths.
The best one for ease of rearing and quality of silk
is Antheraea polyphemus, which is related to the tussah moths.
Silk offers the
spinner a wide range of options, from
the simple to the very challenging.
It can be made into many different
kinds of yarn, from lace weight to
chunky, smooth to novelty. The history
and mystique of silk, along with its
beautiful look and touchable softness,
make it a perfect fiber for many special
projects.
Links:
aurorasilk.com
- Master natural dyer Cheryl Kolander works
with silk in a wide range of forms, from cocoons
to fabric. Cheryl promotes "Peace Silk," where
Bombyx mori are raised and bred without stifling.
habutextiles.com
- Habu Textiles is an excellent source for hard-to-find
specialty silk yarns, and specialty items such
as Japanese silk reel bobbins.
littlebarninc.com
- Little Barn is a good source for raw silk
fiber. They're one of the few places that stocks
Muga from time to time.
thesilkworker.com
- Carol Weymar dyes and sells a range of silk
specialty spinning fibers. Her silk hankies
and caps are particularly renowned.
treenwaysilks.com
- Karen Selk runs the largest distributor of
silk specialty fibers and yarns in North America.
This is the best place to get cocoons, and they
have some great information as well.
wormspit.com
- This is my own website on silk and silkworms.
|